Проблема использования твёрдых топлив для эффективного и экологически чистого производства электроэнергии и тепла может быть надёжно решена при применении водоугольной суспензии, даже в случаях использования в составе исходных материалов низкосортных топлив и различных углеродосодержащих отходов.
Авторы: Карпов Е.Г., Цепенок А.И., Серант Ф.А., Листратов И.В., Радченко С.М, ЗАО «КОТЭС», ЗАО «ЗиО-КОТЭС», г. Новосибирск, Россия ФГУП НПО «Гидротрубопровод», г. Москва, Россия; ООО «НПЦ КаВУТ», г. Барнаул, Россия
Авторы: Карпов Е.Г., Цепенок А.И., Серант Ф.А., Листратов И.В., Радченко С.М, ЗАО «КОТЭС», ЗАО «ЗиО-КОТЭС», г. Новосибирск, Россия ФГУП НПО «Гидротрубопровод», г. Москва, Россия; ООО «НПЦ КаВУТ», г. Барнаул, Россия
Водоугольное топливо, получаемое из смеси молотого угля с водой, известно в мире достаточно давно. В 80-е годы прошлого века в СССР была реализована опытно-промышленная схема получения, транспортировки и сжигания водоугольной суспензии (ВУС). При этом приготовление ВУС велось в Кузбассе (г. Белово), откуда суспензия по трубопроводу длиной 260 км транспортировалась на Новосибирскую ТЭЦ-5, где сжигалась в энергетических котлах большой мощности. Эксперимент проводился начиная с 1987 года. За время проведения эксперимента было сожжено более 50 тыс. тонн ВУС и при этом определилось, что водоугольное топливо имеет ряд преимуществ по сравнению с сухим углем, хотя проявились также и недостатки некоторых технических решений, в том числе:
Преимущества водоугольного топлива состоят в слудующем:
Актуальность использования водоугольного топлива на ТЭС обусловлена появлением новых технологий его приготовления и сжигания, исключающих ранее выявленные недостатки. Суть новой технологии приготовления ВУС состоит в том, что смесь углесодержащих материалов с водой подвергается кавитационному воздействию в специальных аппаратах- кавитационных диспергаторах. Результатом кавитационной обработки, характеризующейся чрезвычайно высоким уровнем местного динамического, компрессионного и температурного воздействия на обрабатываемый материал (до 2000 °С и 25000 кгс/см2), является не только измельчение твёрдого компонента смеси до микронной степени дисперсности, но и появление на поверхности его частиц свойств ярко выраженной гидрофильности. Технологическая схема и общая компоновка узла приготовления КаВУТ приведена на Рис. 1.
Рис. 1. — Технологическая схема и общая компоновка узла приготовления КаВУТ
- громоздкость технологии приготовления ВУС и необходимость химических присадок для обеспечения стабильности суспензии и её пластичности;
- факельное сжигания ВУС в неприспособленных существующих камерных топках потребовало подсветки основного факела высокореакционным топливом. Выявился малый временной ресурс работы форсунок на ВУС и существенный мехнедожог. В экспериментах использовалась ВУС из малозольного длиннопламенного Кузнецкого угля.
Преимущества водоугольного топлива состоят в слудующем:
- отказ от систем конвейерного транспорта топлива и систем пылеприготовления, что отражается на упрощении компоновочных решений ТЭС, снижении стоимости их строительства за счёт исключения традиционных топливоподач с бункерными этажерками и мельничными системами в главных корпусах, оснащаемых аспирационными системами и узлами гидросмыва;
- снижение эксплуатационных затрат на ремонты и обслуживание систем топливоподачи;
- улучшение санитарно-гигиенических условий работы обслуживающего персонала;
- значительном снижении уровня взрывопожароопасности объектов электростанции;
- снижении выбросов вредных веществ, прежде всего оксидов азота.
Актуальность использования водоугольного топлива на ТЭС обусловлена появлением новых технологий его приготовления и сжигания, исключающих ранее выявленные недостатки. Суть новой технологии приготовления ВУС состоит в том, что смесь углесодержащих материалов с водой подвергается кавитационному воздействию в специальных аппаратах- кавитационных диспергаторах. Результатом кавитационной обработки, характеризующейся чрезвычайно высоким уровнем местного динамического, компрессионного и температурного воздействия на обрабатываемый материал (до 2000 °С и 25000 кгс/см2), является не только измельчение твёрдого компонента смеси до микронной степени дисперсности, но и появление на поверхности его частиц свойств ярко выраженной гидрофильности. Технологическая схема и общая компоновка узла приготовления КаВУТ приведена на Рис. 1.
Рис. 1. — Технологическая схема и общая компоновка узла приготовления КаВУТ

В отличие от традиционного ВУС кавитационное водоугольное топливо (КаВУТ) стабильно на протяжении длительного времени (контрольные образцы выдерживались в течение 4-х лет) и пластично без каких-либо присадок при достигнутом содержании твёрдого вещества до 65%.
Технологический процесс приготовления КаВУТ характеризуется низкими удельными показателями энергозатрат (до 30 кВтч/тн) и расхода металла рабочих органов кавитаторов (менее 100 граммов на тонну угля), компактностью технологической схемы, простотой в эксплуатации и ремонтном обслуживании.
Удельные затраты на производство КаВУТ составляют 200 руб/тн.
Удельные затраты на сооружение установки по приготовлению КаВУТ составляют 1,4 млн.руб/т.н в час.
Удельный объём здания установки приготовления КаВУТ 40-50 м3/тн. в час.
Сложности, связанные с попытками факельного сжигания ВУС в неприспособленных существующих камерных топках, определяются необходимостью распыления суспензии до микронных размеров и увеличением времени пребывания частиц в топке из-за повышенного влагосодержания. Поэтому для приготовления ВУС рекомендовались длиннопламенные и газовые (высокореакционные) малозольные угли и именно такие угли достаточно успешно сжигаются в виде ВУС в Китае.
С учётом результатов стендовых сжиганий различных типов водоугольных топлив по различным технологиям, как наиболее универсальный и особенно подходящий для сжигания КаВУТ из низкосортных топлив нами сделан выбор в пользу технологии сжигания КаВУТ в псевдокипящем слое инертного материала. Такой вариант, вследствие высокой тепловой стабильности массы псевдоожиженного материала, позволяет осуществить зажигание и реагирование топлива при более низких, чем при камерном сжигании, температурах. Этот фактор обеспечивает существенное снижение генерации высокотоксичных оксидов азота, чему способствует также повышенное содержание в реакционной зоне паров воды.
С целью обеспечения управляемости процессом горения КаВУТ при пониженной температуре в кипящем слое, максимально возможного снижения образования оксидов азота, но повышения удельной теплопроизводительности топки кипящего слоя нами предложен унифицированный комбинированый вариант, состоящий из топки низкотемпературного кипящего слоя и камерной топки. Для существующих котлов малой мощности предлагается выносить топку кипящего слоя (предтопок) отдельно от камерной топки котла (Рис. 2).
В предтопке с кипящим слоем протекает низкотемпературный процесс предварительной подготовки и газификации топлива в условиях недостатка воздуха (α<1). В камерной топке, в которой создаются, за счёт подачи дополнительного количества нагретого воздуха, условия для полного реагирования горючих веществ, происходит догорание продуктов газификации и мелкодисперсных остатков несгоревшего топлива при более высокой, чем в предтопке, температуре.
Рис. 2- Схема малой промышленной установки по варианту с выносным предтопком для реконструируемых котлов.
Технологический процесс приготовления КаВУТ характеризуется низкими удельными показателями энергозатрат (до 30 кВтч/тн) и расхода металла рабочих органов кавитаторов (менее 100 граммов на тонну угля), компактностью технологической схемы, простотой в эксплуатации и ремонтном обслуживании.
Удельные затраты на производство КаВУТ составляют 200 руб/тн.
Удельные затраты на сооружение установки по приготовлению КаВУТ составляют 1,4 млн.руб/т.н в час.
Удельный объём здания установки приготовления КаВУТ 40-50 м3/тн. в час.
Сложности, связанные с попытками факельного сжигания ВУС в неприспособленных существующих камерных топках, определяются необходимостью распыления суспензии до микронных размеров и увеличением времени пребывания частиц в топке из-за повышенного влагосодержания. Поэтому для приготовления ВУС рекомендовались длиннопламенные и газовые (высокореакционные) малозольные угли и именно такие угли достаточно успешно сжигаются в виде ВУС в Китае.
С учётом результатов стендовых сжиганий различных типов водоугольных топлив по различным технологиям, как наиболее универсальный и особенно подходящий для сжигания КаВУТ из низкосортных топлив нами сделан выбор в пользу технологии сжигания КаВУТ в псевдокипящем слое инертного материала. Такой вариант, вследствие высокой тепловой стабильности массы псевдоожиженного материала, позволяет осуществить зажигание и реагирование топлива при более низких, чем при камерном сжигании, температурах. Этот фактор обеспечивает существенное снижение генерации высокотоксичных оксидов азота, чему способствует также повышенное содержание в реакционной зоне паров воды.
С целью обеспечения управляемости процессом горения КаВУТ при пониженной температуре в кипящем слое, максимально возможного снижения образования оксидов азота, но повышения удельной теплопроизводительности топки кипящего слоя нами предложен унифицированный комбинированый вариант, состоящий из топки низкотемпературного кипящего слоя и камерной топки. Для существующих котлов малой мощности предлагается выносить топку кипящего слоя (предтопок) отдельно от камерной топки котла (Рис. 2).
В предтопке с кипящим слоем протекает низкотемпературный процесс предварительной подготовки и газификации топлива в условиях недостатка воздуха (α<1). В камерной топке, в которой создаются, за счёт подачи дополнительного количества нагретого воздуха, условия для полного реагирования горючих веществ, происходит догорание продуктов газификации и мелкодисперсных остатков несгоревшего топлива при более высокой, чем в предтопке, температуре.
Рис. 2- Схема малой промышленной установки по варианту с выносным предтопком для реконструируемых котлов.

Предлагаемая схема сжигания водоугольного топлива обеспечивает:
На полигоне московского предприятия ФГУП «Гидротрубопровод» многократно проводились эксперименты по приготовлению КаВУТ из различных углей, а также отходов углеобогащения и огневые стендовые испытания двухстадийного сжигания КаВУТ. Эксперименты подтвердили возможность получения устойчивого и управляемого процесса горения с частичной газификацией топлива в кипящем слое первой ступени топки. Огневые эксперименты проведены с использованием различных исходных продуктов, показатели исходных продуктов и готового КаВУТ представлены в Табл. 1.
Табл-1. Качественные показатели исходных углей для КаВУТ, использованных на огневом стенде
- полное его выгорание без мелкодисперсного распыления;
- почти трёхкратное снижение образования оксидов азота относительно факельного сжигания угольной пыли
- широкий диапазон устойчивости горения, исключение необходимости подсветки факела высокореакционным топливом (газ, мазут) на всех этапах горения.
На полигоне московского предприятия ФГУП «Гидротрубопровод» многократно проводились эксперименты по приготовлению КаВУТ из различных углей, а также отходов углеобогащения и огневые стендовые испытания двухстадийного сжигания КаВУТ. Эксперименты подтвердили возможность получения устойчивого и управляемого процесса горения с частичной газификацией топлива в кипящем слое первой ступени топки. Огневые эксперименты проведены с использованием различных исходных продуктов, показатели исходных продуктов и готового КаВУТ представлены в Табл. 1.
Табл-1. Качественные показатели исходных углей для КаВУТ, использованных на огневом стенде

Фотографии процесса горения КаВУТ в кипящем слое режимах полного выгорания и газификации представлены на рис. 3.
В процессе проведения каждого из экспериментов получены продолжительные, устойчивые, хорошо управляемые процессы сжигания КаВУТ, характеризуемые:
Рис. 3 – Процесс горения КаВУТ в предтопке с кипящим слоем: а) режим "полного выгорания" б) режим "газификации".
В процессе проведения каждого из экспериментов получены продолжительные, устойчивые, хорошо управляемые процессы сжигания КаВУТ, характеризуемые:
- стабильностью аэродинамики псевдокипящего слоя;
- эффективностью протекания процесса горения;
- невысоким содержанием вредных примесей в уходящих газах.
Рис. 3 – Процесс горения КаВУТ в предтопке с кипящим слоем: а) режим "полного выгорания" б) режим "газификации".

Таблица 2 Основные показатели горения различных вариантов КаВУТ.
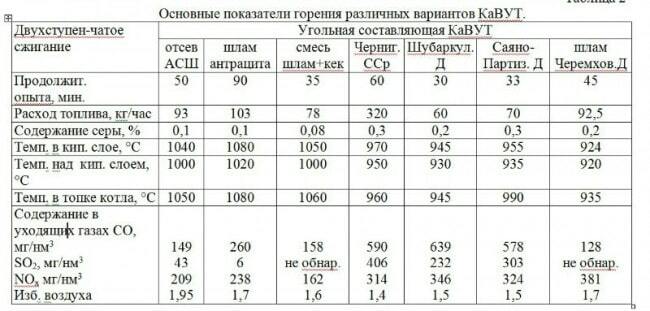
Результаты экспериментов учитывались при выборе режимов работы переводимых на сжигание КаВУТ котлов:
Не так давно появился ещё один очень перспективный вид отходов- нефтяной кокс, являющийся твёрдым остатком глубокой вторичной переработки тяжелых нефтепродуктов. Значительные объёмы получения такого отхода в ближайшей перспективе при особенностях этого продукта отразятся на топливном балансе и оборудовании энергетики.
При малой зольности (<1%) и высокой теплотворной способности (до 8000 ккал/кг) нефтекокс, тем не менее, не относится к высокосортному топливу из-за высокого содержания серы (4÷7 %) и ванадия (до 0,15%). К тому же, незначительный выход летучих (8÷12%) определяет низкие реакционные свойства нефтекокса, что, при высоких коррозионных и шлакующих свойствах, требует специальных методов и устройств для использования его в энергетике. На текущий момент в мире наиболее распространены способы сжигания нефтекокса в котлах, оборудованных топками с циркулирующим кипящим слоем (ЦКС) с вводом в топку сорбента для связывания серы. Также нефтекокс сжигают в смеси с углём в пылеугольных котлах, оснащённых эффективными системами сероочистки и азотоподавления. Затраты на такой комплекс очистки составят не менее 30% от общей стоимости строительства объекта. При этом оптимальных решений проблем шлакования не найдено.
Набор проблем, связанных с использованием нефтекокса в энергетике по ряду показателей сопоставим с проблемами сжигания в энергетических котлах антрацитов и отходов их обогащения, результаты проработок по которым представлены выше. В основе предлагаемой нами технологии сжигания нефтекокса лежит идея получения из него, с использованием кавитационных устройств, водной суспензии и сжигания такого КаВУТ в низкотемпературном кипящем слое инертного материала.
Высокое содержание серы в нефтекоксе может отрицательно сказаться на эффективности использования известных схем мокрых и мокро-сухих способов связывания оксидов серы, оставляя без защиты от сернокислой коррозии хвостовые участки котла (ТВП или РВП, золоуловители и газоходы). Необходимо также принимать в расчёт наличие в составе нефтекокса значительного количества ванадия и обязательной необходимости связывания его оксидов уже на начальных участках топки котла для исключения высокотемпературной ванадиевой коррозии ширмово-конвективных поверхностей нагревая. Для проверки влияния этих особенностей нефтекокса на процесс кавитационной переработки его в КаВУТ и на процесс сжигания полученного топлива проведены стендовые огневые испытания, основные результаты представлены в табл. 3. При этом опробовано использование приготовление и сжигание различных вариантов КаВУТ из нефтекокса:
Таблица 3 Основные показатели опытов со сжиганием КаВУТ из нефтекокса.
- Е-1,0/0,9 для сжигания КаВУТ из высокоувлажнённого шлама обогатительной фабрики разреза ЗАО «Черниговец», перерабатывающей уголь марки СС;
- КВр-3,15 с переводом его на сжигание КаВУТ из отходов технологического процесса обогатительной фабрики ЗАО «Сибирский Антрацит». В настоящее время завершаются пуско-наладочные работы на реконструированном котле КВр-3,15.
Не так давно появился ещё один очень перспективный вид отходов- нефтяной кокс, являющийся твёрдым остатком глубокой вторичной переработки тяжелых нефтепродуктов. Значительные объёмы получения такого отхода в ближайшей перспективе при особенностях этого продукта отразятся на топливном балансе и оборудовании энергетики.
При малой зольности (<1%) и высокой теплотворной способности (до 8000 ккал/кг) нефтекокс, тем не менее, не относится к высокосортному топливу из-за высокого содержания серы (4÷7 %) и ванадия (до 0,15%). К тому же, незначительный выход летучих (8÷12%) определяет низкие реакционные свойства нефтекокса, что, при высоких коррозионных и шлакующих свойствах, требует специальных методов и устройств для использования его в энергетике. На текущий момент в мире наиболее распространены способы сжигания нефтекокса в котлах, оборудованных топками с циркулирующим кипящим слоем (ЦКС) с вводом в топку сорбента для связывания серы. Также нефтекокс сжигают в смеси с углём в пылеугольных котлах, оснащённых эффективными системами сероочистки и азотоподавления. Затраты на такой комплекс очистки составят не менее 30% от общей стоимости строительства объекта. При этом оптимальных решений проблем шлакования не найдено.
Набор проблем, связанных с использованием нефтекокса в энергетике по ряду показателей сопоставим с проблемами сжигания в энергетических котлах антрацитов и отходов их обогащения, результаты проработок по которым представлены выше. В основе предлагаемой нами технологии сжигания нефтекокса лежит идея получения из него, с использованием кавитационных устройств, водной суспензии и сжигания такого КаВУТ в низкотемпературном кипящем слое инертного материала.
Высокое содержание серы в нефтекоксе может отрицательно сказаться на эффективности использования известных схем мокрых и мокро-сухих способов связывания оксидов серы, оставляя без защиты от сернокислой коррозии хвостовые участки котла (ТВП или РВП, золоуловители и газоходы). Необходимо также принимать в расчёт наличие в составе нефтекокса значительного количества ванадия и обязательной необходимости связывания его оксидов уже на начальных участках топки котла для исключения высокотемпературной ванадиевой коррозии ширмово-конвективных поверхностей нагревая. Для проверки влияния этих особенностей нефтекокса на процесс кавитационной переработки его в КаВУТ и на процесс сжигания полученного топлива проведены стендовые огневые испытания, основные результаты представлены в табл. 3. При этом опробовано использование приготовление и сжигание различных вариантов КаВУТ из нефтекокса:
- КаВУТ 0- без присадок и пластификатора;
- КаВУТнк- с добавкой 0,6 % пластификатора С3;
- КаВУТMg- с присадкой MgO в соотношении Mg:S=1:1 и добавкой 1,0 % С3.
- КаВУТCa1- с присадкой Ca(OH)2 в соотношении Ca:S=1:1 и добавкой 0,8 % С3.
- КаВУТСа2- с присадкой Са(ОН)2 в соотношении Са:S=1,5:1 и добавкой 0,6% С3.
Таблица 3 Основные показатели опытов со сжиганием КаВУТ из нефтекокса.

Проведенные испытания подтвердили технологическую работоспособность и экологическую эффективность двухступенчатого сжигания КаВУТ из нефтекокса.
По результатам экспериментальных и расчетных исследований разработаны схемы сжигания и конструкции топочно-горелочных устройств для котлов большой и малой мощности.
При переводе котлов на сжигание КаВУТ, как правило в котельном отделении, вместо бункеров и питателей угля появляются баки (силосы) для жидкого КаВУТ и компактные трубопроводные системы. Подача и распределение КаВУТ осуществляется с помощью насосов. Пример компоновки бакового хозяйства в отопительной котельной ЗАО «Сибирский Антрацит» представлен на Рис. 4.
Рис. 4 — Расположение бакового хозяйства КаВУТ в отопительной котельной.
По результатам экспериментальных и расчетных исследований разработаны схемы сжигания и конструкции топочно-горелочных устройств для котлов большой и малой мощности.
При переводе котлов на сжигание КаВУТ, как правило в котельном отделении, вместо бункеров и питателей угля появляются баки (силосы) для жидкого КаВУТ и компактные трубопроводные системы. Подача и распределение КаВУТ осуществляется с помощью насосов. Пример компоновки бакового хозяйства в отопительной котельной ЗАО «Сибирский Антрацит» представлен на Рис. 4.
Рис. 4 — Расположение бакового хозяйства КаВУТ в отопительной котельной.

При переводе котлов малой мощности с имеющейся решеткой кипящего слоя реконструкция топочной камеры имеет минимальный объем и заключается в установки форсунок для подачи КаВУТ (Рис. 5). КаВУТ подается через прямоточный канал форсунки и разбрызгивается за счет подачи первичного воздуха от дутьевого вентилятора.
Сам котел также принципиально не изменяется, дополнительно предусматривается только установка подогревателя вторичного воздуха. Общий вид реконструированного котла и его фото на объекте представлены на Рис. 6.
Рис. 5 — Установка форсунок подачи КаВУТ из отходов углеобогащения на котле КВр-3,15.
Сам котел также принципиально не изменяется, дополнительно предусматривается только установка подогревателя вторичного воздуха. Общий вид реконструированного котла и его фото на объекте представлены на Рис. 6.
Рис. 5 — Установка форсунок подачи КаВУТ из отходов углеобогащения на котле КВр-3,15.

Рис. 6 — Общий вид реконструированного котла КВр-3,15 (а) и его фото на объекте (б).

Для котлов большой мощности требуется замена нижней части топочной камеры с установкой решетки кипящего слоя и специальных вихревых горелок. Под решетку подводится первичный воздух, над решеткой организуется подача инертного материала в слой и топлива (50-70% от общего расхода на котел), а также возврат несгоревших частиц. Для растопки котла и разогрева слоя инертного материала требуется установка растопочных газовых горелок. Выше, над слоем, устанавливаются основные комбинированные горелки, в которые подается остальные ~30-50 % топлива.
На рис. 7 представлен вариант реконструкции нижней части топки газомазутного котла паропроизводительностью 500 т/ч для его перевода на сжигание КаВУТ из нефтекокса.
Рис. 7 — Реконструкция нижней части топки котла паропроизводительностью 500 т/ч с установкой воздухораспределительной решетки кипящего слоя.
На рис. 7 представлен вариант реконструкции нижней части топки газомазутного котла паропроизводительностью 500 т/ч для его перевода на сжигание КаВУТ из нефтекокса.
Рис. 7 — Реконструкция нижней части топки котла паропроизводительностью 500 т/ч с установкой воздухораспределительной решетки кипящего слоя.

Вихревые горелки, в данном конкретном случае, могут работать на газе и обеспечивать требуемую нагрузку котла без подачи КаВУТ.
В целом при реконструкции котла сохраняется его профиль, каркас, компоновка поверхностей нагрева и прочие основные узлы. Изменения преимущественно касаются схемы газовоздухопроводов, установки системы улова и возврата несгоревших коксовых частиц и реконструкции топочной камеры. Общий вид реконструируемого котла представлен на Рис. 8.
Рис. 8 — Общий вид газомазутного котла паропроизводительностью 500 т/ч при его переводе на сжигание КаВУТ из нефтяного кокса.
В целом при реконструкции котла сохраняется его профиль, каркас, компоновка поверхностей нагрева и прочие основные узлы. Изменения преимущественно касаются схемы газовоздухопроводов, установки системы улова и возврата несгоревших коксовых частиц и реконструкции топочной камеры. Общий вид реконструируемого котла представлен на Рис. 8.
Рис. 8 — Общий вид газомазутного котла паропроизводительностью 500 т/ч при его переводе на сжигание КаВУТ из нефтяного кокса.

Таким образом, актуальность и возможность перевода котлов малой и большой мощности на сжигание отходов углеобогащения и других низкосортных топлив на сегодняшний день не вызывает сомнений, а имеющиеся наработки показывают целесообразность переработки этих топлив в КаВУТ.